How the Future of Origami Engineering is Unfolding
Origami, the Japanese art form that dates at least to the 17th century, creates unique patterns and shapes from paper folding. Today, origami is inspiring engineers to design active materials and smart structures that bend, stretch and curve, overcoming traditional design constraints and rendering products and systems with remarkable performance characteristics and features. Perhaps the most ubiquitous example is the amazingly compact automobile airbag, though origami-inspired engineering is also making commercial inroads in the energy, apparel and healthcare industries. Reflecting emerging interest in the field, the U.S. National Science Foundation funded eight U.S. universities to advance origami engineering into the realm of reconfigurable, smart, structures and self-assembling systems.
Folding, far beyond paper
“Origami engineering can meet the demand, across multiple industries, for products and systems with very complex applications,” said Mary Frecker, a professor of mechanical engineering and biomedical engineering at the Pennsylvania State University, one of the schools to receive an NSF research grant. “Origami enables products with the ability to fold and then unfold on demand — at any time.” To create such products, engineers are experimenting with active materials like magneto-active elastomers, which are comprised of magnetic filler particles — such as barium ferrite — embedded in an elastomer matrix and which display a special ability to curve and rotate when a magnetic field is applied. Polymer synthetic compounds featuring extremely high energy density are also favorites in the origami design community due to the ability of the material to compress and stretch in the presence of a voltage. While such materials are almost magical in how they morph into different shapes and patterns, the challenge for engineers is create a system that is structurally sound and can be fabricated for practical use.
“Traditional origami art uses paper; however, most engineering applications require materials with finite thickness to provide the necessary strength and stiffness to achieve a desired functionality,” said Frecker. “Our analysis of experimental designs shows that different activation processes determine different folds, curves and deformation in the material structure.”
Medical marvels
As researchers continue to create new structures that stand up to practical use, some companies have placed origami-inspired designs into the commercial marketplace, realizing the benefits of products and systems with unique folding capabilities. GE Healthcare recently collaborated with Brigham Young University (BYU) on a cover for the extension arm of an X-ray machine used in hospital operating rooms. The shroud expands and contracts like a musical accordion to shield the sterile field in the OR from the non-sterile environment of the extension arm. The shroud is made of Tyvek®, a type of synthetic paper produced by DuPont. GE required a design improvement over the plastic drapes commonly used to shroud the moveable C-arm; the drapes needed to be replaced every time the device rotated in and out of the sterile field, adding time as well as cost to surgical procedures. The design of the shroud was complex. In order to accommodate the needed motion and geometry of the X-ray machine arm, the BYU team developed an adjustable shroud based on a crease pattern named Miura-ori. Named after the Japanese astrophysicist Koryo Miura, the Miura-ori method has inspired the field of systems design, allowing engineers to fold and unfold rigid and thick surfaces in different directions and continuous motion. Another healthcare application for origami engineering is in the area of surgical probes, forceps and other instruments that have the ability to enter an opening in the body in a narrow and compact state and unfold after insertion. Origami-based engineering may also play a role in improved biomedical stents.
“GE needed a design for the shroud that maintained the sterile field during all movements and positions of the extension arm,” said Larry Howell, a professor in the Department of Mechanical Engineering at BYU, also a recipient of one of the NSF grants.
“After several concepts were evaluated and tested, an origami-based design was selected.”
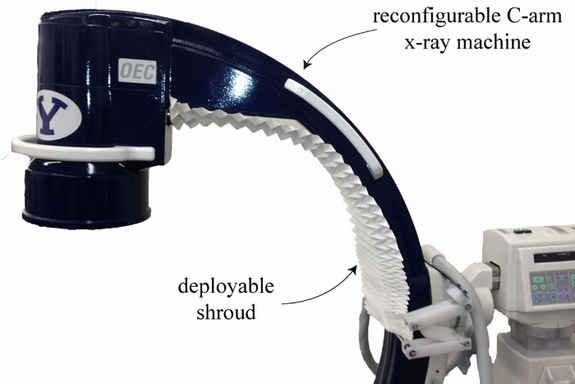
The expanding role for Origami Engineering
Beyond the medical field, origami-inspired products include telescopes, protective covers for automobiles, sporting goods, kayaks, solar arrays, appliance drawers and temporary shelters. Solar arrays represent an example of deployable membranes that allow engineers a range of design flexibility, including low friction joints, low material volume, controlled buckling, and extensive spanning ability. In the area of sporting goods and apparel, industrial design students at BYU, in collaboration with the consumer products firm Tessel Supply, have adapted origami in the design of a novel backpack. The distinguishing features of the backpack are the triangular meshes that allow the bag to conform to the articles within, reducing jostling of the contents and providing protection against damage. Combining form and function, the backpack matches careful engineering with pleasing aesthetics and comfort. “These and other products present evidence that foldable solutions are viable in engineering design,” said Howell. “Origami art will continue to inspire products that need to be portable and deployable”. According to Frecker at Penn State, one area of growing interest is in self-folding structures, as well as deployable large-scale systems for space exploration. There is also an emerging focus on applications that combine electrical, magnetic and thermal means to activate materials to enable origami-based design. There were 28 presentations on origami at the 2014 ASME Design Engineering Technical Conferences — interest in the field is surging.
Story Source: The above story is based on materials published on The Next Generation blog. This version of the article was originally published on Live Science written by John Varrasi. Images credit NASA and Brigham Young University. Note: Materials may be edited for content and length.